Így áll egy gumigyár
A Bridgestone tatabányai gyárában jártunk, hogy megnézzük, hogyan születnek a gumik. Azt nem tudták megígérni, hogy fotózhatunk is, de majd meglátjuk. Ám a Bridgestone nem viccel akkor, amikor kifejleszti a csúcstechnikát - és akkor sem, amikor meg akarja őrizni ezt titoknak.
Gábor! Ír valamit itt a képernyő sarkában, hogy frissítés, vagy mi a szar. Gáááboooor! Hallod? Az operátor ideges hangját elnyelte a zakatoló gyár, a hatalmas monitoron vibráló termelési számok mindegyike zölden világított, egyedül az a pici ördög, az a kis felugró ablak jelezte, hogy valami nincs rendben. Az egér finom kattanása szinte feloldódott az ajtókilincs nyikorgásában, Gábor lépett be a terembe. Azonnal látta, hogy elkésett, kezébe temette az arcát és erőtlenül rogyott le a székre.
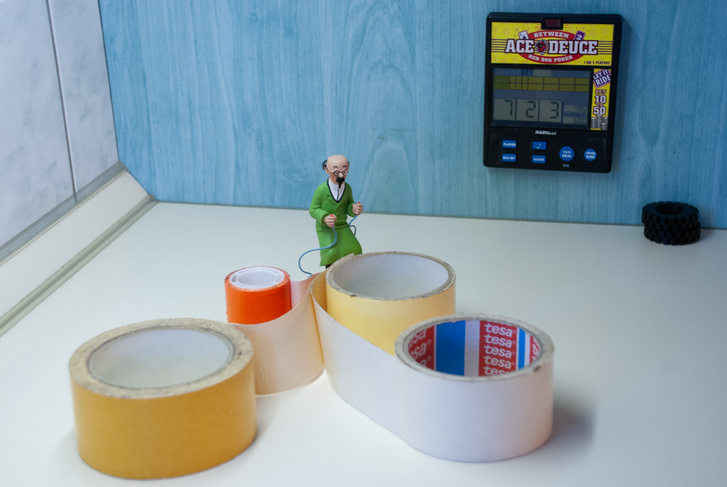
István. – sziszegte ujjai közül enerváltan. Ma jönnek az újságírók, akiknek hetek óta szervezzük ezt a gyárlátogatást. Egyszer már lemondtuk. Mit fognak látni? Üldögélő embereket? Pihenő gépeket? Végre lett volna esély, hogy ne csak elcsépelt PR-cikkek szülessenek a gyárról, erre te mindent elrontasz egy átkozott mozdulattal.
Hatalmas szusszanással állt le az üzem, a szerszámok halk ropogással törekedtek a környezeti hőmérséklet elérésére, szögre kerültek a védőszemüvegek, csend lett. A dohányzásra kijelölt helyen egy ütemre pattintott szikrát néhány tenyérbe rejtett öngyújtó, visszafogott beszélgetés jelezte, hogy a hét középső napja nem kispéntek, és a munka is mindjárt folytatódik. Gábor és István még mindig szótlanul nézték egymást.
A Bridgestone új téligumijának apropójából érkeztünk a gyárba, ha István keze lassabb, akkor egy rendes gyárlátogatásra. Két kiállított Blizzak LM005 abroncson kívül sokat nem érintkeztünk az újdonsággal, de abban is biztos vagyok, hogy aki téligumi vásárlása előtt áll, és eljutott eddig a cikkben, az simán megtalálja a teszteket is a neten. A Bridgestone új gumija számos szaklap tesztjén, több kategóriában kiváló eredményeket ért el, abszolút ajánlott kategória.
Nekünk az lenne a feladatunk, hogy a kulisszák mögé tekintve a gumiválasztás purgatóriumában vulkanizálódó olvasó érzelmére és értelmére hassunk a tények, érdekességek kendőzetlen feltárásával. Gyermeki izgalommal érkeztem én is a gyárba, láthatósági mellény, munkavédelmi sisak és munkavédelmi cipő került a testemre, komoly kalanddal kecsegtetett a négy kártyacsippantásra lévő üzem.
A legdurvább Michelineket nálunk gyártják
Egy munkahely, ahol tilos nyakkendőt viselni. Viszont meg lehet tudni, hogy mitől szőrös a gumi, és mitől kerül akár 200 ezerbe darabja.
Akkor kezdett erős Szabó család-szag terjengeni, amikor fotózási tilalom mellett beléptünk a leállított gyárba. Magyarországon négy gumiabroncs-gyár működik, ebből kettőben már jártunk: a Hankook legalább mutatott gyáron kívül valamit, de bent tilos volt fotózni; a Michelinnél csak simán tiltották a fényképezést, de legalább informatív fotókat adtak; a Bridgestone tehát magasra tette a lécet az álló gyárban tiltott fotózással. Vajon mit találnak majd ki az Apollo Tyres-nél? Most mindenesetre a fotózást próbáltam házilagos eszközökkel megoldani, a gyár sajtóosztályától kapott képeken nem mutatnak sok mindent.
Az öntömítő abroncs titka: a trutyi
...ekkor az ember beverte a szöget a gumiba, majd kihúzta, és mentünk tovább. Defekt nincs, amíg gumi a gumi, nem kell javítani.
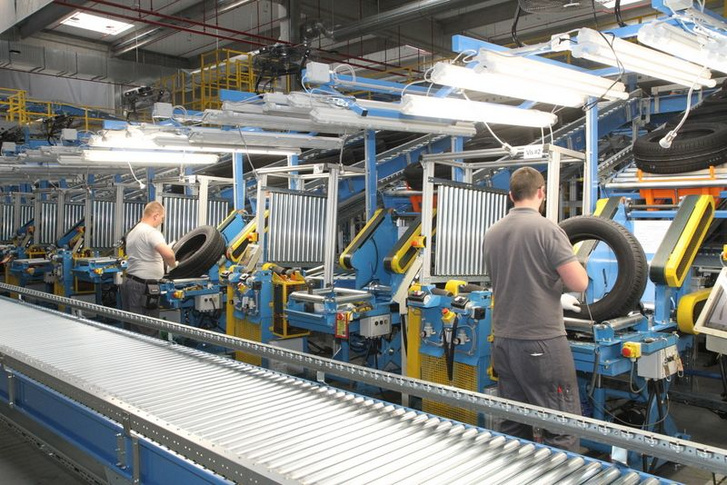
Ezerkétszáz alkalmazottja van a tatabányai gyárnak, nyolcszáz ember dolgozik a termelésben, hatalmas az üzemcsarnok. Gépek, konvejorok, hordozótekercsek mindenhol. Vezetőnk készségesen magyarázta a megnémult üzem kihűlt gépei között sétálva a gumigyártás folyamatát. A gyárba több forrásból érkeznek a korommal színezett gumi- és szintetikus gumialapanyagok. Európában nincs divatja a fehér peremű abroncsoknak, ezért nem is kell a feketén kívül más szín. Egy átlagos gumiabroncs 12-18 különböző alkatrészből épül fel, a Bridgestone üzeme két típusú eljárást alkalmaz az összeépítésre. Az egyik, a legfejlettebb B.I.R.D. technológia, ahol a gépet kívülről etetik a nyersanyaggal és a végén kiesik a kész gumiabroncs, a másik a hagyományos technológia, ahol különböző állomásokon különböző részfeladatok készülnek el és a vulkanizáló állomáson sütik véglegesre a pizzát. A B.I.R.D. gépek, ha jól vannak beállítva húsz perc alatt összeállítanak egy gumiabroncsot, aztán már lehet is vulkanizálni.
Eltérő gumiból készül a légzáró réteg, más anyag kell az oldalfalhoz, eltérő összetételű a futófelület is. A különböző rétegeket más és más hordozóanyagra kell feltenni, van, ami textilszerű tekercsen utazik, van olyan, ami műanyag fólián. Az abroncs végszerelése a különböző rétegek egymásra tekerésével történik.
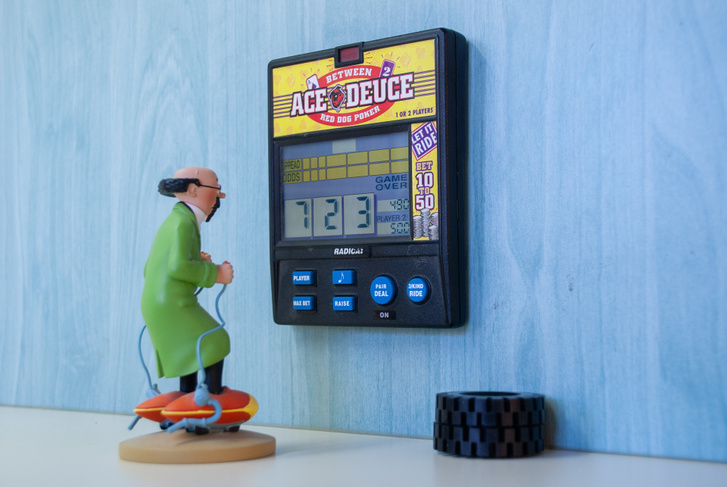
Ha elkészült a tekercs, akkor bekerül a vulkanizáló szerszámba, ami úgy néz ki, mint egy trilex keréktárcsa negatívja. Szegmensekből áll össze, ezek közé szorul be a gumi 150-180 fokos hőmérsékleten, nagyjából húsz percre. Ennyi idő alatt tökéletesen térhálósodik a kaucsuk, a képlékeny gumikeverékből rugalmas és kopásálló gumi lesz.
A vulkanizálás után fontos lépés a gumi megfelelő lehűtése, majd legvégül a legújabb technológia szerinti végellenőrző berendezés rostálja a frissen elkészült abroncsokat. Ezt úgy kell elképzelni, hogy egy összetett futószalagrendszeren haladnak a gumik és különböző szenzorok, kamerák segítségével válogatják ki a hibás abroncsokat további vizsgálatra, javításra vagy selejtezésre.
Az utolsó művelet azonban az emberi kézé. Nincs az a gép, ami az emberi tapintásnál pontosabban tudná észrevenni az apró esztétikai hibákat. A futófelületen lévő kis fehér karika az végellenőrök pecsétje.
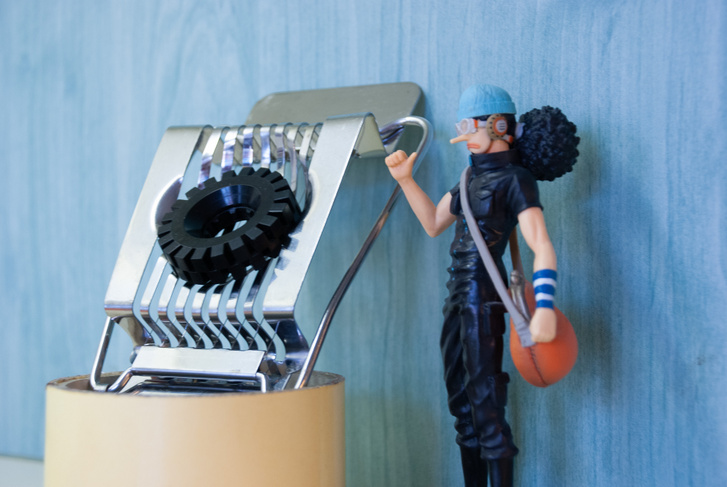
A japán precizitás és a magyar mérnöki zsenialitás boszorkánysága rejtve maradt előlünk, pedig van tesztlabor is a gyárban, ott aztán érdekes dolgokról vallhatnak az abroncsok. Hátha egyszer beengednek oda minket.
(Gábor és István természetesen kitalált személyek, sőt, az illusztrációkon szereplő apró bábuk sem dolgoznak a Bridgestone-nál.)

Az oldalról ajánljuk
- Hírek
Trump vámjai jelenthetik az utolsó szöget az Alfa Romeo és a Maserati koporsójában
A Stellantis egyre kevésbé teheti meg, hogy életben tartja a küszködő márkáit.
- Hírek
A BMW áprilisi tréfája a legfájdalmasabb
Nem jó poén, mert ezeket meg kell csinálniuk.
- Hírek
Kínai és angol technológiával, arab pénzből érkezhet a következő McLaren
Ezzel mindenki jól járna.
- Olajdoktor
Forrest Gump motorolajat keres
És mert hogy már milliomos voltam, de imádtam füvet nyírni, attól fogva ingyen csináltam.
- Hírek
Trump vámtarifái az amerikai autóipart is kegyetlenül megszívatják
Nincs olyan amerikai autó, ami megúszná a vámokat.
- Hírek
Brutál gyorsulást és horror árcédulát ígér az Icon restomod Ford Broncója
A legtöbb katalógusadat kiváló, de ennek megkérik az árát.
- Tesztek
A tárgyiasult modern burzsoáziaTeszt: Renault Rafale 300 - 2024.
Az autóipar a megszokásokról és a trendekről szól, amelybe a Renault Rafale beleillik, de egy picit mégis más.
- Technika
Most szombaton MűhelyPRN 300. adás élőben!
A 300. részt élő közvetítéssel ünnepeljük, tartsatok velünk!
- Nepperűző
Örökölt kabrió hírhedten hitvány motorral - mennyiért szabadulhatok meg tőle?
Esztétikailag sérült, eszegeti az olajat, néha kerreg. Sosem adtam el autót, ez mennyit érhet?
- Hírek
Megjött a Tesla negyedéves eredménye és gyalázatos
Ennél mindenki jobbra számított.
- Hírek
Nyert egy 911 GT3 RS-t, részegen rommá törte
Az új tulaj nem volt okos, így hamar szomorú véget ért a pompás nyereményautó.
- Hírek
Verstappené a pole pozíció a Japán Nagydíjon
Ez pályafutása 41. pole pozíciója.
- Hírek
A Stellantis leépítéssel és gyártásleállítással válaszolt az amerikai vámokra
Gyorsan alkalmazkodnak.
- Gumidoktor
6 éves a téligumi, merjem még használni?
A szett hibátlanul viselkedik, a profilmélysége is rendben, de aggaszt a kora. Használhatom még vagy már kuka?
- Hírek
Így néz ki a használtautó-cunami a Dacia hazájában
Ömlik a használt autó a szomszédba.
- Hírek
Szétrúgott egy Cybertruckot, de biztosan megbánta
A férfi a tulaj szeme láttára abuzálta a Teslát, végül a Cybertruck kamerái buktatták le.
- Hírek
Pánikszobát kapnak a Tesla-kereskedések az erőszakos ügyfelek és vandálok miatt
Így védenék az alkalmazottakat a támadásoktól.
- Hírek
Alig 40-nel döcögött az autópálya középső sávjában egy fogalmatlan suzukis bácsi
De legalább végig indexelt. Részletkérdés, hogy nem akart sávot váltani.
- Hírek
Súlyos baleset történt a Forma-1-es Japán Nagydíj szabadedzésén, ezért félbeszakították
Az Alpine pilótája 260 km/h-nál dobta el a versenyautót.
- Hírek
Lenyűgöző, nyúlánk kupét és kabriót mutatott a Genesis
Mindkét pompás vonalú alkotás a Genesis G90-en alapul.
- Közélet
A BYD szerint csak kevés kínai gyártó marad majd Európában
Elképesztően tartós akkumulátort és villámgyors töltést is ígér a BYD, Szegeden pedig sokkal több készül, mint egy egyszerű gyáregység.
