Az ország nagy részének sokáig az Opel Astra jelentette az új nyugati autót, ha a Suzuki Swiftet nem soroljuk ide. A hazai gyártásnak köszönhetően kellően olcsó tudott lenni az F-Astra, így a különböző kivitelek elárasztották az utakat. Bár sokáig hagyták gyártásban idővel átálltak a kor színvonalának megfelelő típusokra, így jutott el a szentgotthárdi gyár a tavalyi bővítéshez. Ekkor sikerült helyet szorítani az SWE-nek is. De mi az az SWE?
Az SWE, teljes nevén Simulated Work Environment, egy szimulációs munkakörnyezet. Ezt úgy kell érteni, hogy elkerítettek egy részt, a régi és az új gyárrészek között, ahol felépítettek egy mini gyártósort és hozzá egy kvázi tantermet asztallal, székekkel táblával és projektorral. Félreértés ne essék, a cél nem a sajtó előtt haknizás, hanem mindenki, aki az Opelnél dolgozik, részt vesz itt egy egynapos tréningen, legyen gyári munkás, vagy akár pénzügyes. Ennek egyfelől van egy csapatépítő jellege, másfelől így mindenki megismeri a gyárban is használt GMS minőségbiztosítási rendszert.
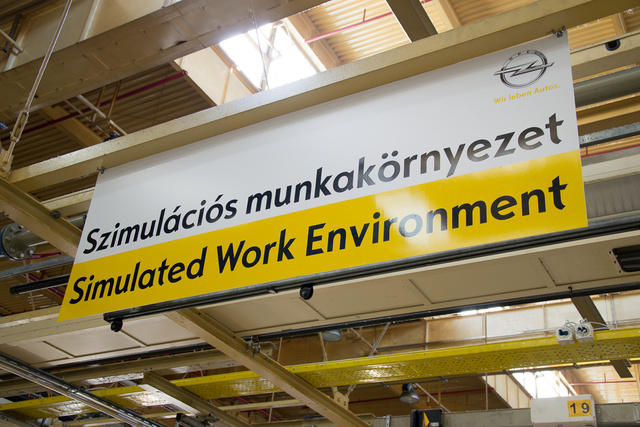
GMS? Azt eszik vagy isszák?
Ha valaki elkezd minőségmenedzsmenttel foglalkozni, szinte biztos, hogy az adott könyv, jegyzet, pdf vagy dia első oldalain a minőségmenedzsment unalmas történelmével találja magát szemben. Ez a mai szemmel már-már magától értetődő folyamat, hogy hogyan fejlődött az ellenőrzés szabályozássá, a szabályozás pedig teljes minőségbiztosítási rendszerré. Autós nyelvre fordítva, hogy jutunk el a Ford T-Modelltől a Toyota Corolla legendás megbízhatóságáig. Utóbbi gyártó alkalmazott ugyanis először teljes minőségbiztosítási rendszert az autóiparban. A TPS, azaz a Toyota Product System lényege a hatékonyság maximalizálása, és eközben a biztonság előtérbe helyezése. És mint tudjuk, jobbtól lopni nem szégyen. Különben, hogy terjedtek volna el a világot előre lendítő megoldások? Tudta ezt a General Motors is, amikor a Toyota mintájára megalkotta saját vállalatirányítási rendszerét, a GMS-t.
A GMS teljes minőségbiztosítási rendszer, vagy ahogy magát nevezi gondolkodásmód öt alappillérre épül: emberek bevonása, egységesítés, beépített minőség, rövid átfutási idő és folyamatos fejlesztés. Ezek a hangzatos szavak a valóságban egy szigorú utasításrendszert takarnak, és ez működik a hamarosan kilencszázról ezerhatszáz fősre bővített szentgotthárdi Opel gyárban is.
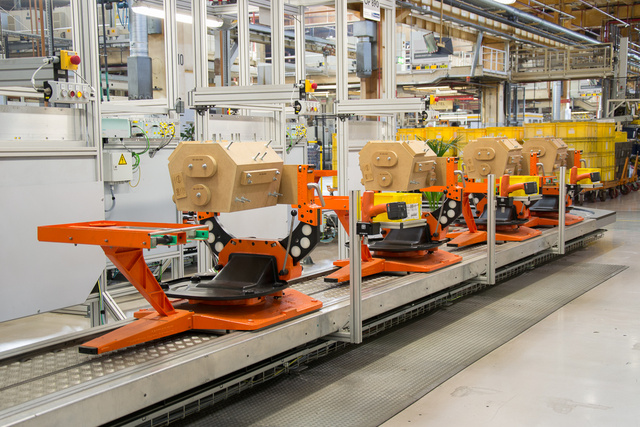
A betanított munkások felváltva végzik a különböző feladatokat: két óra hengerfej felrakás után például jöhet két óra injektor felszerelés, persze mindeközben rengeteg ellenőrzés. Mivel a termelés folyamatos, nincs álló munkafázis. Ha bárkinek bármilyen típusú problémája van, azt jelzi egy gomb megnyomásával. Egy központi táblán felgyullad a területet jelző lámpa, és a területhez tartozó szignál csendül fel. Ekkor a csapatvezető segít megoldani a problémát, de ha olyan a helyzet ideiglenesen át is veheti a munkát. Ezt a visszajelző rendszert egyébként Andonnak hívják. Külső szemmel még viccesnek is tűnhet, hogy egy autógyár működésének olajozottságáért egy nagy, az uszodai eredményjelzőkre emlékeztető, tábla felelős, sok színes felvillanó lámpával, miközben a kaputelefonokhoz hasonló gépi dallamok harsogják olykor túl egymást. A rendszer hatékonyságát pedig az is bizonyítja, hogy a gyáriak szerint a következő lépcsőfok a zéró hiba lenne. Én hiszek is nekik, főleg azok után, hogy én is beálltam a gyártósor mellé.
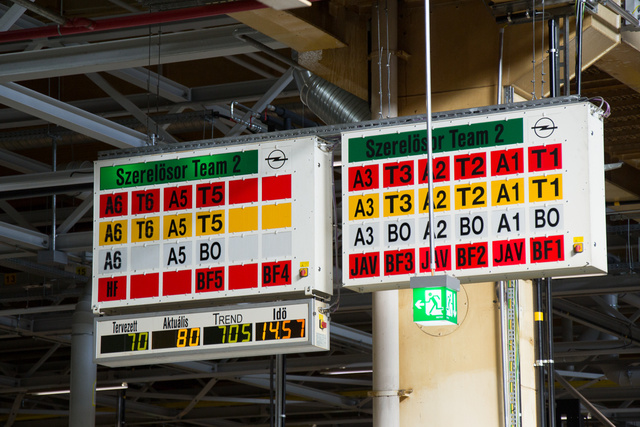
Amikor az újságíró csapattal megérkeztünk, első feladatunk volt, hogy megnézzük a gyári viselkedésre vonatkozó videót, de attól, hogy ezt láttuk, még felelőtlenség lett volna velünk veszélyeztetni a motorgyártást, ezért a gyáron belül felépített szimulációs központban várt minket egy program.
A tréninget ketten tartották, Károly és Zoli. Mindketten a kezdetek óta dolgoznak a szentgotthárdi gyárban. Végigjárták a szamárlétrát, most balesetvédelmi, problémamegoldó és szimulációs tréningeket tartanak. Abszolút összeszokott párost alkotnak, olyanok, mint Hacsek és Sajó, Frédi és Béni, vagy Stan és Pan, rutinosan dobják fel és csapják le egymás a labdáit. Miután bemutatkoztunk és megismertük a GMS-t jött az éles bevetés gyártósor. A gyártósor, amin fából vannak a motorok. Igen, fából. Hogy miért? A munkamechanizmust így is meg lehet ismerni, de nincsenek részletek, amik elvonják a figyelmet. Most mindenki azt hiszi, hogy biztos az egész unalmas és erőltetett, de nem.

A munkához kerettörténet is tartozott, az üzbég Opel gyár kért tőlünk motorokat. Két három fős csapatban dolgoztunk, a cél a tizenhat motor összeszerelése volt. Minden munkaállomásnak megvolt a maga feladata, legjobb tudásunk szerint csavaroztuk le-fel az alkatrészeket helyettesítő fatáblákat, de csak tizenegyet sikerült összehoznunka megadott idő alatt. Ezután jött a fejlesztési fázis, optimalizáltuk a különböző állomások feladatmennyiségét, a szerelési sorrendet, és a lehető legkevesebb idő- és energiabefektetést szem előtt tartva alakítottuk ki a munkakörnyezetünket. Második nekifutásra pedig összejött a tizenhat motor. A fiktív üzbég kollégák pedig nagyon boldogok voltak. Eddig egy jó buli volt, de csak ezután jöttek az igazi csavarok, csapágyak és injektorok, összeraktunk egy valódi motort is.
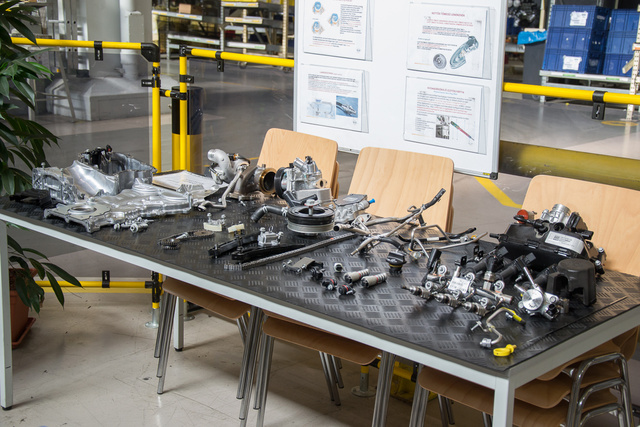
A szentgotthárdi Opel gyárat 1992-ben nyitották meg, majd 18 évnyi sikeres működés után 2010-ben érkezett el az idő a teljes megújulásra és bővítésre. Lényegében egy újabb gyárat építettek a gyáron belül, ez a Flex. Itt, az idei évtől kezdve új generációs, középkategóriás motorokat gyártanak rugalmas termelési rendszerben, és jövőre érkeznek a kisebb háromhengeresek is a palettára. Egy ilyet Ecoflex motort raktunk össze mi is.
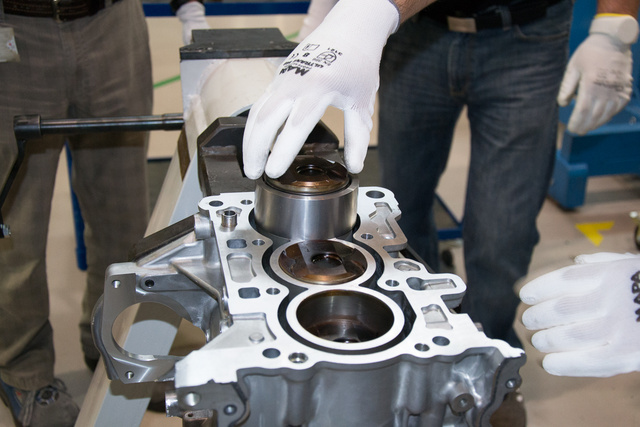
Sokak szemében a mai motorok már az űrtechnikához hasonlítanak, pedig nem, igaz minden sokkal kompaktabb. Egy háromhengeres ezres turbós benzinest raktunk össze. A munka nagy részét persze a tréningvezetőink végezték, de egyszer-egyszer mi is besegítettünk, a fennmaradó időben pedig tátott szájjal figyeltünk. Kiindulásnak adott volt a blokköntvény egy forgatható állványon, és két asztal tele a beépítendő alkatrészekkel. Nagyjából másfél óra alatt készült el a teljes motor. Rajta mindennel, ami azért felelős, hogy ez az ezres háromhengeres nagyobb autók megmozgatásához megfelelő teljesítményt adhasson le. Ebben főként a turbónak, a nagynyomású injektoroknak, és a megnövekedett olajnyomás hatására elfokoló vezérműnek van szerepe. A motor egyébként láncos, nem szíjas, előnye, hogy a csereperiódusa örökélet plusz egy nap. Feltettük a kuplungot és a hagyományos (nem kettős tömegű) lendkereket is, de olajjal és vízzel nem töltöttük fel a kész motort, és a csavarokat sem húztuk nyomatékra. Felesleges is lett volna, másnap jött a következő csoport, addig még újra szét is kellett szedni.
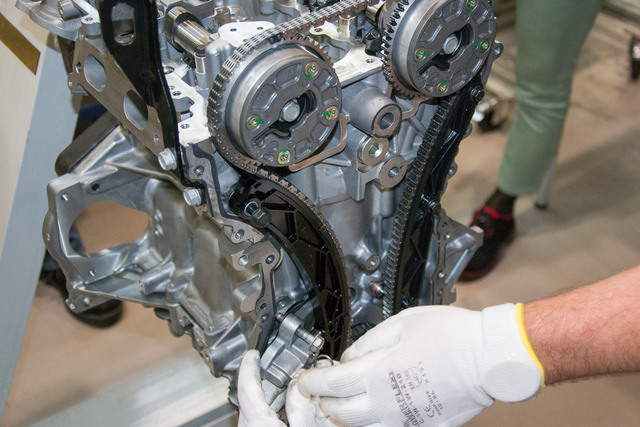
Flexet mindenkinek?
A Flex projekt összberuházása megközelítőleg 700 millió euró. Ennek keretein belül idén januárig 400 embert vettek fel, és ez a szám azóta is nő, sőt várhatóan nőni is fog 2015 végéig. Az új munkaerő döntő többsége a gyártósorok mellett fog dolgozni. A fejlesztések végén a gyár várhatóan 70 ezerrel több motor előállítására lesz képes éves szinten, mint korábban.Az ezres SIDI májusban jön, és az Opel több modelljében is találkozhatunk majd vele, például az Adamban. A teljesítménye alapján az 1.4-es és 1.6-os benzines szívó motorokat hivatott kiváltani a kis háromhengeres. Papíron hasonló, vagy még jobb eredményeket produkálnak a kis turbósok, ha a leadott teljesítményt, a nyomatékot, vagy a károsanyag kibocsátást hasonlítjuk össze az előddel, de sokkal kíméletesebb üzemet követelnek meg. És ha ez nincs meg, a javíttatás is többe fog kerülni.

Az autó és motorszerelésről mindenkinek rendezetlen, olajos garázsok jutnak eszébe, pedig ha részt vehetnének egy ilyen programon, akkor lehet, hogy nem idegenkednének a témától. Kellően interaktív, tudományos, és érdekes. Ha ilyen lenne egy középiskolás fizikaóra nem a bölcsész szakokra lenne túljelentkezés.

Az oldalról ajánljuk
- Tesztek
Méltó Transit-e az E-Transit?Menetpróba: Ford elektromos Transit termékcsalád
A napfényes Barcelonában próbáltuk ki a Transit termékcsalád villanyosított tagjait.
- Hírek
Neked is kéne ez az összkerekes-terepezős Swift
A holland Suzuki képviselet követte el.
- Hírek
A kutyának sem kell? - Az orosz autópiac végzetesen bezuhant
A helyzeten valószínűleg csak az állami beavatkozás segíthet.
- Vélemény
10 sportautó, amit becsülettel befejeztek
Karottával összegyűjtöttük azokat az autókat, amik úgy hagyták el a gyárat, hogy neked már csak élvezned kell a tudásukat.
- Tesztek
Ezt a kompótot már érdemes eltenniHasználtteszt: BMW 323ti 1998
Emiatt már érdemes lesz kijönnöd a Parkoló Parádéra is, mert ritkább, mint egy M3.
- Hírek
Piastri közepesen izgalmasan, de komolyabb nehézségek nélkül nyerte a Szaúdi Nagydíjat
Így már ő vezeti a világbajnokságot.
- Gumidoktor
Öreg autóra apró, de király gumi kéne. Van ilyen?
Huszonéves Hyundai-ra szeretnék olyan gumikat, amik a lehető legjobban viselkednek. Mit válasszak a szűk kínálatból?
- Hírek
Nem fogy elég jól a Cybertruck, árkedvezmények mellett csökkentik a termelést is
Közben csoportos kereset indult a Model Y kilométerszámlálója miatt, viszont a Model 3 akkuja elég jól bírja a kilométereket.
- Hírek
Hatalmas időmérős csata után Verstappen indulhat poleból a Szaúdi Nagydíjon
Norris elmérte a falat, így csak a tizedik helyről indulhat.
- Közélet
Hárommillióért minden van: szoci veterán, hodály családi és csótány limuzin is - Murvaélet #6
Három millióért kerestünk használt autókat és egy kicsit már a veteránozásba is belekóstoltunk.
- Hírek
Videó: Közveszélyes szellemi rövidnadrágok között autózunk
Chevrolet Matizzal randalírozó idiótán és F Astra kabrióval veszélyesen közlekedő kreténen is szörnyülködhetsz.
- Hírek
Élő adásban történt súlyos motoros baleset a Bajna-Héreg szerpentinen
A motoros valószínűleg nem megfelelően választotta meg a sebességét.
- Hírek
Néhány Ford megállíthatatlan (rossz rajtuk a fék, visszahívják őket)
A veszélyes probléma több mint 123 ezer Fordot és Lincolnt érinthet.
- Hírek
Elképesztő értékvesztés tapasztalható az Audi E-tron GT-knél
A számok nagyon csúnyák és nagyon elbizonytalaníthatják az újautó-piac szereplőit.
- Technika
40 féle mód, ahogy automata váltót lehet csinálni
Karok, pöckök, tekerők, pixelek, semmi nem szab határt.
- Szerelem
Ezek voltak a kedvenc MűhelyPRN epizódjaink
Életveszélyes autók, tigrisbukfenc, személyes érintettség, és persze a Csirkecsontó! Hat év terméséből mazsoláztunk nektek.
- Hírek
A Renault ananászból akar díszítőelemeket gyártani a beltereihez
Alternatívákat keresnek a bőrre és a műanyagra.
- Hírek
Ilyen sakktáblát is csak a Rolls-Royce csinálhatott!
Formabontó, nagyon minőségi kidolgozású, és természetesen nem árulják el az árát.
- Hírek
Súlyos baleset az Üllői úton: egy Nissan 300ZX-et tarolt le a villanyoszlop
Az autó, ami annak idején annyira erős volt, hogy a japán Közlekedési Minisztérium utasította a gyártót, hogy csökkentse a teljesítményét.
- Olajdoktor
Szivárog az olaj a Kia turbójából, a márkaszerviz szerint ez normális
Keveset futott, nem túl öreg autóról van szó. Tényleg normális, hogy szivárog az olaj turbónál?
- Hírek
A Huawei és a Chery közös újdonsága 1673 kilométeres hatótávot ígér
A Luxeed R7 nem csak hajtásláncot, de kiemelkedően igényes futóművet is ígér!
- Hírek
Nissan: naná, hogy visszatér a GT-R, semmi kétség
Már a Nissan célpontja is megvan: a Porsche 911-et szeretnék majd megverni a jövő GT-R-ével.
- Nepperűző
Szívóbenzines után villanyautóra váltanék. Vagy egy másik szívóbenzinesre?
Tényleg 2 liter benzin áráért lehet 100 kilométert megtenni? A racionalitást vagy a kisördögöt válasszam?
- Technika
Géppornó: hány liter folyadék kell egy 150 tonnás dömperbe?
Sok, ráadásul 500 üzemóránként cserélni kell. Autókhoz szokott ésszel nehéz felfogni a Kress 200C III számait.
